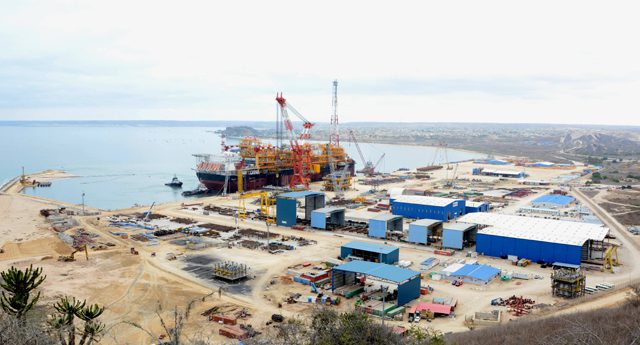
(c) SBM Offshore
In 2008, the Angolan town of Porto Amboim located approximately 280 kilometers south of Luanda in the Kwanza Sul province was essentially a beach town with a small marine terminal which had fallen into significant disrepair.
Fast forward five years and this quiet coastline has now developed into one of the most modern fabrication and integration yards in Africa thanks to investment from Angola’s state-owned national oil company Sonangol, SBM Offshore, and South Korean shipbuilder, Daewoo Shipbuilding & Marine Engineering.
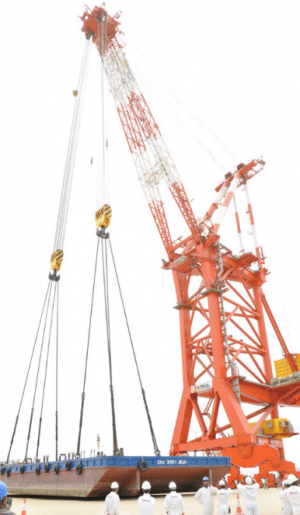
With 2500 ton lifting capacity, Jamba the strongest and biggest crane of its kind in Africa, image (c) SBM Offshore
Covering an area of 175,000m2 and with 490 meters of quay side dredged to a 10m water-depth, Porto Amboim Estaleiros Navais (Paenal) is the only yard on the West African coast capable of berthing Very Large Crude Carriers (VLCCs). In addition, the port can accommodate extreme heavy lifting operations with their 2500 ton crane named Jamba.
“Paenal was established to meet a need to develop manufacturing technology and integration of modules in floating production, storage and offloading units,” comments Yard Managing Director Cesar Guerra. Paenal is capable of producing up to 10,000 tons of modules per year according to an emailed statement.
“One of the main strategies for the joint venture,” notes JV partner SBM Offshore, “was to plan for the needs of a community in close parallel to the yard’s development. One key issue was providing employment for a disadvantaged generation following a turbulent period in the country’s history, as a result of over 35 years of civil war. Finding the required skilled workers locally who met international standards required an initiative and investment by SBM and its partners.”
After establishing a dedicated training school in Porto Amboim, SBM notes the yard’s workforce has grown exponentially to almost 1,200 employees, 85 percent of which are Angolan nationals.
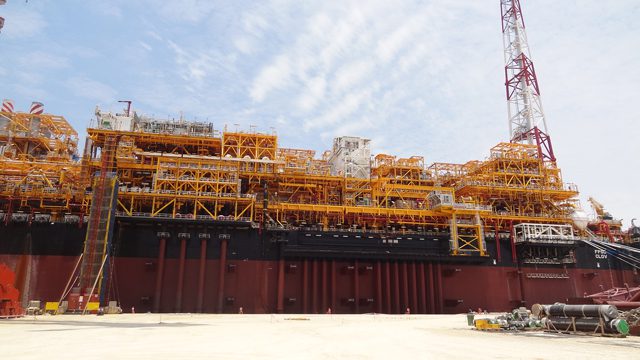
(c) SBM Offshore
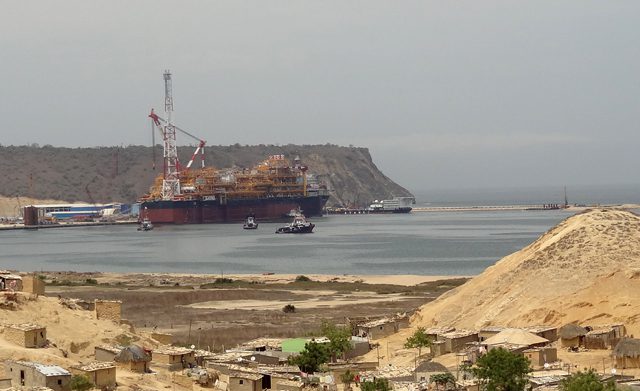
(c) SBM Offshore
On 5 December, Total hosted the naming ceremony of their CLOV FPSO, a vessel which had arrived at Paenal in mid-November after a 18,520km voyage from DSME shipyard in South Korea. A week later, Jamba lifted a 1,836 ton module and placed it aboard the CLOV FPSO. This operation marked the first time a topside module integration had been performed in Africa.
The CLOV FPSO will be operated by Total at Block 17 offshore Angola and is the fourth deepwater project to be undertaken at Block 17 following Girassol, Dalia and Pazflor.
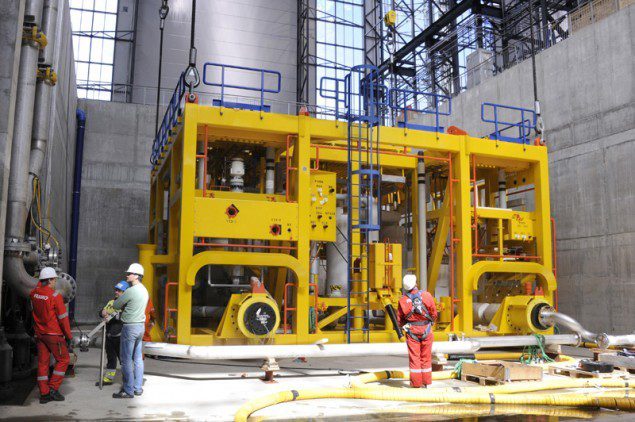
Image (c) Total
Total notes that CLOV will be their first project to use a deep-water helical-axial multiphase pump system in order to optimize the recovery of hydrocarbons within reservoirs where pressure conditions are less favorable and the oil more viscous.
Located at a depth of 1,170 m, the powerful pump system will optimize recovery of hydrocarbons from the Orquidea and Violeta oil fields.
According to project deputy director, François Bichon, these pumps “will compensate for the gradual fall in pressure in the oil fields by helping to propel the more viscous oil up from the seabed to the production and storage unit on the sea’s surface – the FPSO.”
“The multiphase helical-axial structure is a high-performance design which prevents any loss of load and enables the rotor to evacuate a mix of several (even highly variable) fluids at high speed,” adds François Bichon.
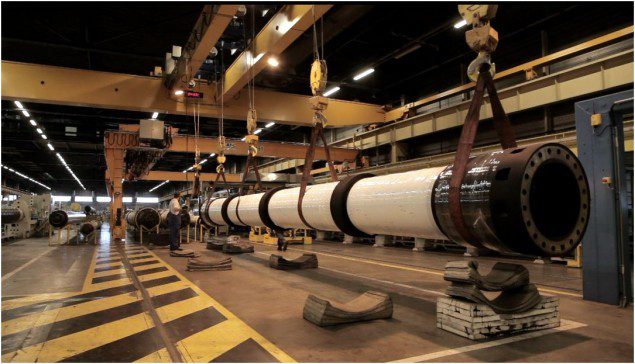
(c) Total
New oil offloading technology
Total notes that the CLOV FPSO will use Trelleborg’s reinforced rubber Oil Offloading Lines (OOLs) with internal diameters of 24 inches, which is wider than those deployed on previous projects. These wider diameter lines will enable the more rapid transfer of crude oil at a lower pressure, and with less required electrical power according to Total engineer, Cyril de Coatpont.
These two 2-km long pipes are also more resistant as well notes Coatpont,
“They are designed to withstand pressure levels of 30 bars. They have to be reinforced so as to be able to withstand the water hammers that can accidentally occur during offloading operations. It’s also worth remembering that these pipelines have been designed to last at least 20 years.”